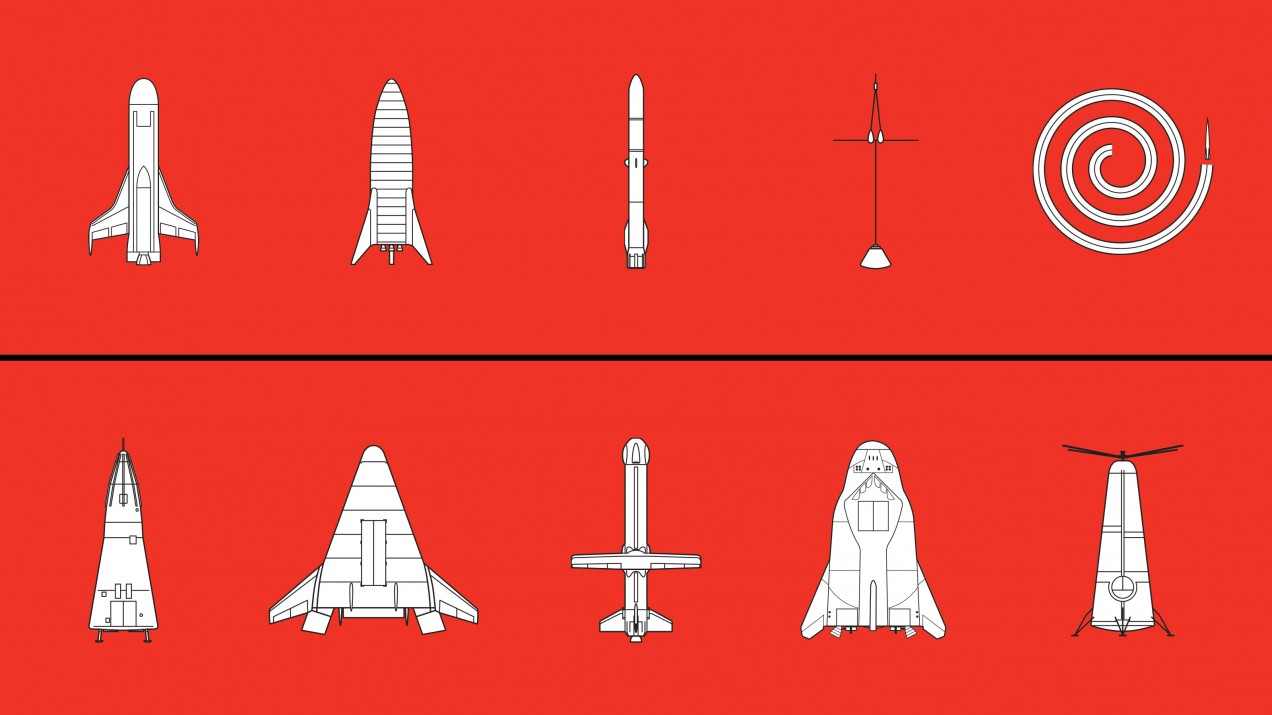
In the closing decades of the last century and the first decades of this one, the average cost of launching a kilogram into Earth orbit simply would not change. The price stubbornly hovered above $10,000, and new idea after new idea failed to break the impasse.
This stymied innovation—after all, if it’s expensive to launch something, it becomes tricky to take other kinds of risks. But opinion was split: Had things stagnated because there was never enough money to see ideas through? Or was it because other improvements—in, say, materials science or autonomous navigation—were insufficiently mature?
All that has changed in the last few years as new craft broke the deadlock, most notably SpaceX’s Falcon Heavy, which is about a tenth as costly, per kilogram, as its closest competitor.
Now the central question is whether this is the start of a new plateau or whether, as Elon Musk hopes, it signals ever cheaper launches and ever more space innovation. The success or failure of these systems will help find an answer.
Ever since the 1960s, engineers have dreamed of a spaceplane that can be reused frequently in a way that makes space travel more like air travel. Nobody has yet come close. The XS-1, being built by Boeing for the Pentagon research agency DARPA, is supposed to be able to make 10 flights in 10 days, taking up to 5,000 pounds (2,268 kilograms) to orbit for under $5 million. Test flights are planned for 2020.
Starhopper is a prototype of the first stage of SpaceX’s planned Big Falcon Rocket, or BFR. The company plans to use it to send people to Mars, as well as to run half-hour shuttle services on Earth between cities like New York and Shanghai. BFR’s payload capacity is about three times that of the Falcon Heavy, though Elon Musk has said he believes it will cost less to build. An early version of Starhopper successfully completed a tethered test flight in Texas in April.
This rocket has a payload capacity by weight similar to that of the Falcon Heavy, but it is far wider at seven meters in diameter. That means it has twice the usable volume. Its first stage will fly back to be reused, much like the failed Baikal booster (below). Blue Origin, which is building the rocket, is tight-lipped on test flight dates but is competing for an Air Force contract that would require launches as soon as 2022.
Even if rockets can be reused and achieve economies of scale, fuel is still a major cost. Tethers seek to change this in two different ways. One approach works like swinging a rope, transferring momentum from one end to the other. Tethers Unlimited, a startup, hopes to use this technique to “catch” satellites that don’t have enough energy to get to orbit, and give them an extra boost. Another type of tether would use Earth’s magnetic field to boost the orbit of satellites attached to either end of it. Some test flights have already taken place, and the next is scheduled for June.
Tethers can transfer momentum between objects already in space—but what can you do while you still have the ground to push against? That’s the plan for Spinlaunch, a startup that raised $40 million in venture funding in 2018. The company broke ground on a launch facility in New Mexico in May and plans to launch its first satellites in 2022. It wants to fling as many as five satellites a day to the edge of space using powerful turbines and small onboard rockets—sort of the opposite of a tether elevator.
Single-stage-to-orbit has long been a goal of rocket designers, since avoiding multistage rockets would make things cheaper, faster, and more reusable. The small-scale DC-X from McDonnell Douglas flew several suborbital flights, but the program was canceled before a full-scale, orbit-capable version could be built. It was a victim, depending on whom you ask, of immature technology or of shortsighted bureaucrats. Several Delta Clipper engineers now work for Blue Origin, whose New Shepard rocket is said to be inspired by the DC-X.
NASA spent over a billion dollars on the X-33, a half-scale suborbital version of what would have been the Venture Star. The full-size craft would have been comparable in size to the space shuttle, and the agency even built a dedicated $32 million “spaceport” for it at Edwards Air Force Base in California. But NASA and Lockheed Martin, the company that built the X-33, had many design disagreements, and the program was canceled before the rocket ever flew.
The Baikal booster, designed in the 1990s as a reusable first stage for the Russian Angara rocket, was an idea before its time. Like the first stage of SpaceX’s Falcon rocket, the Baikal was supposed to fly back to be used again. But unlike the Falcon first stage, which uses the same rocket to land that it used to take off, the Baikal had an additional jet engine for landing, which added weight and complexity.
In the wake of the 1986 explosion of the space shuttle Challenger, the HL-20 was designed to safely and cheaply carry passengers to the space station Freedom. Neither it nor the HL-42, a scaled-up successor, ever made it to space. However, Sierra Nevada’s Dream Chaser spacecraft, which is based on the HL-20 design, is slated to deliver cargo to and from the International Space Station starting in late 2020.
Another failed single-stage-to-orbit idea, the Roton, made by Rotary Rocket, stands in the Mojave spaceport as a warning and inspiration to would-be space pioneers. By making the rocket spin rapidly, engineers hoped to eliminate the need for costly and complicated pumps. A prototype made three test flights in 1999, but it was difficult to control. The company ran out of money before the kinks could be worked out.