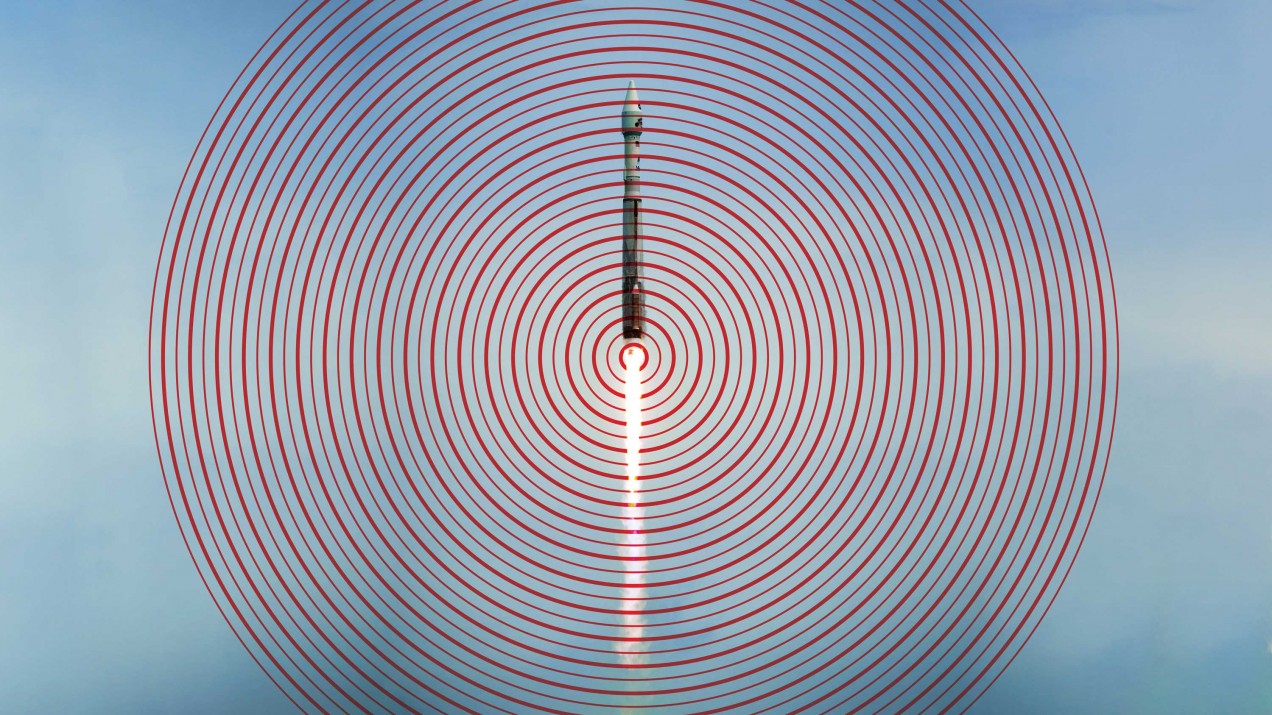
An hour before sunset on May 24, 2000, an unusual rocket took off from Launch Complex 36 at Cape Canaveral Air Force Station. Like most rockets, the Atlas 3 had inherited its design from an intercontinental ballistic missile—in this case, from America’s first such missile, designed to threaten the Soviet Union with nuclear annihilation. This was not unusual. But the rocket had a new first stage, one that was considerably more powerful than those it replaced. The RD-180, as the engine is called, was built by NPO Energomash in a factory outside Moscow. In a marriage that would have been unimaginable at the height of the space race, a Russian engine was powering an American rocket.
In the two decades since, 83 more such rockets have taken off from Florida.
On the Atlas 3 and its successor, the Atlas 5, the RD-180 carried at least 16 American spy satellites to orbit, along with 13 military communications satellites, a half-dozen GPS satellites, two military weather satellites, and three missile warning satellites, designed to detect rocket launches from, among other countries, the one where it was built. It launched four American Mars missions. NASA’s launch of New Horizons to Pluto in 2006 and Juno to Jupiter in 2011 were both made on the back of the RD-180.
The RD-180 is remarkable not only for the geopolitical peculiarities of its rise to prominence, but because it was in many ways simply better than any other rocket engine of its time. When, in February 2019, Elon Musk announced a successful test of SpaceX’s Raptor engine, which is intended to power the company’s next-generation rocket Starship, he bragged of the high pressures reached in the Raptor’s thrust chamber: over 265 times atmospheric pressure at sea level. Raptor, he said on Twitter, had exceeded the record held for several decades by the “awesome Russian RD-180.”
After Russia annexed the Crimea in 2014, the RD-180’s days as a staple of American rocketry were numbered. Defense hawks had long been uncomfortable with the arrangement, but the engine was both very good and, given its capability, cheap—and so it stayed. But as relations with Russia frayed, congressional opponents of the engine, led by Senator John McCain, succeeded in passing a prohibition against the engine’s use in American rockets after the end of 2022. This has forced the Air Force to find a new rocket to succeed the RD-180-powered Atlas 5.
All of which raises a question: How did a decades-old Russian engine become the bar against which America’s best rocket scientists measure themselves?
If you want to understand what made the RD-180 such a good engine, it helps to understand that there is a great deal of craft involved. Though hundreds of people collaborate on rocket engines, having someone with an instinct for good design in charge is vital: the trade-offs are too complex to be figured out by brute force or by committee. In the case of the RD-180, that someone was named Valentin Glushko.
After the USSR lost to America in the race to the moon, designing the best possible rocket engine became “a national priority,” according to Vadim Lukashevich, an aerospace engineer and Russian space historian. Soviet leaders wanted to build the world’s most powerful rocket, the Energia, to sustain their space stations in Earth orbit and to lift the Buran, a would-be Russian space shuttle. Glushko was given resources to build the best engine he could, and he was good at building engines. The result was the RD-170, the RD-180’s older brother.
The RD-170 was among the first rocket engines to use a technique called staged combustion. The US space shuttle main engine, also developed in the 1970s, was another. By contrast, the F-1 engines in the first stage of the Saturn V rocket, which launched Apollo to the moon, were of an older, simpler design called the gas-generator engine. The key difference: staged-combustion engines can be more efficient, but they’re at greater risk of exploding. As William Anderson, who studies liquid-fueled rocket engines at Purdue University, explains, “The rates of energy release are just extreme.” It takes someone with a really astute imagination, Anderson says, to understand the crazy stuff that’s going on inside rocket engines’ combustion chambers. In Russia, that astute person was Glushko.
To understand why Glushko’s engines were such an engineering achievement, we need to get a little bit technical.
There are two key measures of a rocket’s performance: thrust, or the amount of force a rocket exerts, and specific impulse, a measure of how efficiently it uses its propellants. A rocket with high thrust but low specific impulse won’t reach orbit—it would have to carry so much fuel that the weight of the fuel would necessitate more fuel, and so on. Conversely, a rocket with high specific impulse but low thrust would never leave the ground. (Such rockets work well in space, though, where a steady push suffices.)
A rocket engine, much like an aircraft jet engine, burns fuel together with an oxidizer—often oxygen—to create hot gas that expands down and out of the engine nozzle, accelerating the engine the other way. Unlike jet engines, which get oxygen from the air around them, rockets need to carry their own oxygen (or other oxidizer), since in space, of course, there isn’t any. Like jets, rockets need a way to force the fuel and oxygen into the combustion chamber at high pressure; all else being equal, higher pressure means better performance. To do that, rockets use turbopumps that spin at hundreds of rotations per second. The turbopumps are driven by turbines, and they, in turn, are powered by pre-burners, which likewise burn some fuel and oxygen.
The crucial difference between staged-combustion engines like the RD-180 and gas-generator engines like the Saturn’s F-1 lies in what happens to the exhaust from those pre-burners. While gas--generator engines dump it overboard, staged-combustion engines reinject it into the main combustion chamber. One reason for doing this is that the exhaust contains unused fuel and oxygen—the pre-burners can’t burn it all. Throwing it away is a waste, which matters in a rocket that also has to lift every pound of fuel and oxygen it’s going to use. But reinjecting the exhaust entails delicately balancing the relevant pressures and flow rates so that engines don’t blow up. It requires a whole series of turbopumps to make it work. Teams of experts typically need a decade or more of simulation and testing to figure out how to get it right.
The RD-170 and RD-180 have another advantage. They are oxygen--rich, which means exactly what it sounds like: they inject extra oxygen into the system. (The space shuttle main engine, by contrast, is a fuel-rich engine.) Oxygen-rich engines tend to burn cleaner and to ignite more easily. They also make possible higher combustion--chamber pressures, and thus better performance—but they are more prone to explode, so for decades there weren’t any major efforts to make them work in the US. “There was so much invested in the shuttle that no one at NASA wanted to talk about developing an oxygen-rich staged-combustion engine,” says Anderson. “Oxygen will burn most things if you provide a spark.” This requires great care in the materials used to build the engine, and even greater care in making sure no foreign materials—such as specks of metal debris—ever make their way into it. “The more we learn about the physics of what goes on inside a combustion chamber, the more we realize how unsteady it really is,” says Anderson.
If the RD-170 was arguably the best rocket engine of its generation, the space shuttle main engine was arguably second best (and was substantially more expensive to make). Neither lived up to its potential. The space shuttle engine was stuck with a lemon of a vehicle, which was much more cumbersome than its designers had hoped it would be. The RD-170, on the other hand, flew only twice: once in 1987 and once in 1988. Though developing it had been a national priority, by the time Glushko proved that it worked, the Soviet Union was about to fall apart.
The 1990s were a turbulent time in Russia, especially for the space program. To survive without government financing, newly privatized aerospace firms turned to the commercial market.
That’s when Jim Sackett, an engineer who’d been working for Lockheed at NASA’s Johnson Space Center in Houston, moved to Moscow. Lockheed became interested in using oxygen-rich staged combustion to power the next generation of Atlas rockets, with which it planned to compete for Air Force and NASA contracts.
Sackett, who was put in charge of Lockheed’s Moscow office, was tapped to approach Energomash, a post-Soviet space industry firm that came to own the RD-170 and related engine technology. Energomash enthusiastically welcomed Lockheed’s interest. But the RD-170 was too powerful: the Atlas rockets Lockheed was looking to send into space were considerably smaller than the Energia, for which the RD-170 had been designed. So Energomash essentially cut the engine in half—the firm drew up a proposal for a two-chamber derivative of the four-chamber RD-170 that could be used in the Atlas. This was the birth of the RD-180.
The relationship required remarkable integration between Russian and American military--industrial contractors. Lockheed set up an office at Energomash, in a Moscow suburb. It was a huge operation, Sackett remembers. “They’ve got a metallurgy plant there, so they forge their own metals,” he says. “They have all their own machine shops, all of their own test facilities. It is a lot of stuff, all of it under one roof. And eventually, all of it turns into a rocket engine.”
It took about a year of daily, in-depth technical meetings between Sackett’s team and Energomash executives and engineers to understand whether or not the proposed purchases of RD-180 engines would work. Lockheed wanted a small, no-commitment deal. Energomash held out for a long-term arrangement. The contract was signed at the end of a marathon six-hour session in 1996, Sackett says. The result: a 101-engine, billion-dollar deal.
The US Air Force, Lockheed’s main customer, demanded access to 10 key technologies needed to produce the RD-180, in case relations with Russia ever foundered and America had to make the engines itself. It was a big ask. The US was after a crown jewel of Soviet space technology, and the Russian government was not thrilled. “But they saw no alternative,” Sackett says, “because the country did not just have a change of heart, they went broke. They just went flat broke. This is how they saved the company.”
Though more attention has been paid to American-Russian cooperation on the International Space Station, in many respects the RD-180 collaboration went deeper. After all, the space station is not crucial to the national security of either country, while reconnaissance and communications satellites are.
Now that relations between the two countries have frayed, Sackett argues, the US could just manufacture the RD-180 domestically. The engine’s critics say it would be astronomically expensive to do so. But the cost “shouldn’t be astronomical!” Sackett says. “We have smart people here, and we have the recipe! This is exactly why we identified and negotiated for those 10 key manufacturing technologies, so that we could take the drawings and the notes and then go build them.”
That’s not likely to happen, in part because after decades of stagnation, American companies are finally working on engines that just might be better than the RD-180.
An engine’s performance has profound influence over the design of the rocket above it. So when Congress mandated that the Air Force stop using the RD-180, this provoked a competition not just for a new engine, but for a whole new rocket. Such a competition was inevitable—after all, designs don’t last forever. But because designing new engines and rockets is expensive and time consuming, the timing for making a switch is always politically contentious. The congressionally mandated RD-180 ban forced the issue.
There are four serious contenders to build that new rocket: SpaceX, Blue Origin, the United Launch Alliance (a Boeing–Lockheed Martin joint venture known by its initials, ULA), and Northrop Grumman. Two of them will be chosen, on the theory that having two winners creates ongoing competition, while naming one would result in a monopoly that could then turn around and gouge the Air Force. Thousands of jobs are at stake: if ULA loses, it may go out of business.
The New Glenn, Blue Origin’s entry in the competition, uses the BE-4, Blue Origin’s newest and most powerful engine. (As does ULA’s rocket—the two firms are simultaneously competitors and business partners.) The designs of both the BE-4 and SpaceX’s Raptor are informed in crucial ways by the RD-180. The BE-4 is an oxygen--rich staged-combustion engine, like the RD-170 and RD-180. The Raptor, meanwhile, resembles the RD-180 in that it feeds the pre-burner exhaust into the combustion chamber—ensuring that almost all the fuel and oxidizer stored in the rocket’s tanks are used to generate thrust. However, the Raptor relies on a tweak to Glushko’s approach: both fuel-rich and oxidizer-rich flows power its turbopumps—theoretically resulting in maximal efficiency.
In a way, the BE-4 and Raptor are like an attempt to build a better violin than Stradivarius did, using modern methods. Blue Origin and SpaceX have access to better diagnostics and more sophisticated simulation techniques than Glushko did. They also have another design feature important to the American Air Force: they’re made in the US.
Possibly the greatest technical advantage these new engines have over the RD-180 is that they use methane as fuel rather than kerosene, as the RD-180 does. Kerosene can gunk up the works of an engine after repeated use. Methane has higher specific impulse, and burns cleaner. It is also much easier (in principle) to synthesize on Mars, which Musk aims to do.
Neither new engine has yet reached orbit. SpaceX is planning test flights of its Starhopper rocket, which will eventually be powered by three Raptors, for this summer. These flights will be short hops, a few thousand feet in the air above SpaceX’s test site in Texas. Blue Origin is also testing the BE-4 in Texas, and has started building a factory in Alabama where it will manufacture the engines. It has rented Launch Complex 36, where the RD-180 first took flight, from the Air Force and plans to launch the New Glenn there in 2021.
Energomash, meanwhile, is desperately hoping that the Russian space program will again start using its engines. Some 90% of its production has gone to the US in recent years, says Pavel Luzin, a Russian space industry analyst. Like its American counterparts, Energomash now risks being made obsolete by Musk and Bezos—who, with their freedom from legacy design constraints and willingness to spend money and take risks, have finally jolted rocket engine design out of decades of stasis.
Matthew Bodner is a journalist in Moscow who writes about aerospace and the military.